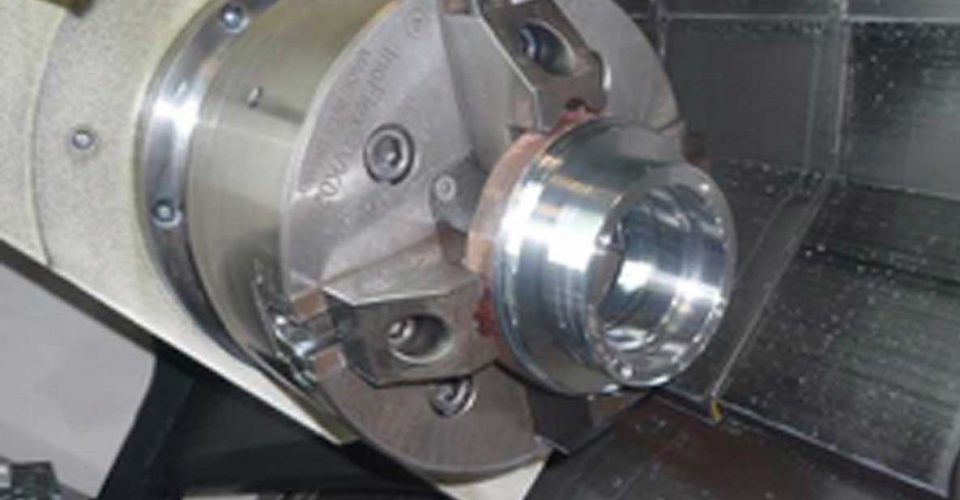
Einsatz von INOFlex®-Spannfutter sorgt für weniger Rundheitsabweichungen
Antriebstechnik-Hersteller verbessert Formgenauigkeit im Lagersitz
Bei geringen Unregelmäßigkeiten oder asymmetrischen Formen stoßen herkömmliche Futter schnell an ihre Grenzen: Während herkömmliche 3-Backenfutter sich nur selten für die Spannung von eckigen Körpern eignen, haben nicht ausgleichende 4-Backen-Spannfutter den Nachteil der statischen Überbestimmung – nicht alle Backen liegen an. Dies führt dazu, dass die zu bearbeitenden Teile nicht zentrisch gespannt werden können. Der hohe Spanndruck bei 2- und 3-Backen-Spannfuttern verursacht bei dünnwandigen Bauteilen große Rundheitsabweichungen – so auch bei der STÖBER ANTRIEBSTECHNIK GmbH & Co. KG. Aus diesem Grund informierte sich der Elektronik-, Motoren- und Getriebehersteller Anfang 2016 über Alternativen zu bestehenden gängigen Spanntechnologien. Dabei wurde er auf das InoFlex-Spannfutter der HWR Spannmittel GmbH aufmerksam: ein 4-Backen-Spannfutter, das über eine ausgleichende zentrische Spannung verfügt. Das bedeutet, dass die jeweils diametral gegenüberliegenden Backen paarweise an das Werkstück heranfahren. Auf diese Weise kann garantiert werden, dass sowohl die Bauteile zentrisch gespannt sind als auch alle Backen greifen; und das mit gleicher Spannkraft. Die Form des Werkstücks spielt hierfür keine Rolle, was eine Anpassung der Parameter für unterschiedliche Gussteile unnötig macht. Durch die Erweiterung von drei auf vier Spannpunkte ließ sich zudem die Rundheit deutlich verbessern. So konnte Stöber die Qualität der Produkte bei gleichzeitig verkürzter Rüst- und Spannzeit steigern.
Im Stammhaus der Stöber Antriebstechnik GmbH & Co. KG in Pforzheim werden bereits seit mehreren Jahrzehnten erfolgreich Getriebe, Motoren und Getriebemotoren hergestellt. Für diese werden in der mechanischen Fertigung direkt vor Ort verschiedene Gussrohlinge gedreht und gefräst. Anfang 2016 fiel dem Unternehmen jedoch ein Optimierungspotential im Bereich der Drehbearbeitung auf: „Zum Drehen von gegossenen und geschmiedeten Rohteilen mit unbearbeiteter Spannfläche haben wir bis letztes Jahr herkömmliche 2- und 3-Backenfutter eingesetzt“, beschreibt Volker Manz, Produktionsleiter bei Stöber Antriebstechnik GmbH & Co. KG, die Ausgangssituation. „Diese hatten den Nachteil, dass sie nach einem Nestwechsel neu eingerichtet werden mussten, da die Gusschargen gewisse Unterschiede zueinander haben.“ Dadurch verlängerte sich die Bearbeitungszeit pro Charge deutlich. Außerdem kam es vor allem bei asymmetrischen und dünnwandigen Rohteilen immer wieder vor, dass die Backen nicht richtig griffen. Zum sicheren Spannen musste als Konsequenz ein zu hoher Spanndruck eingestellt werden. „Dies führte zu Verformungen und somit zu Rundheitsabweichungen“, so Manz weiter.
Vier diametral ausgleichende Spannbacken für mehr Flexibilität
„Meine Kollegen aus der Zentralen Planung Technik sind Anfang letzten Jahres über Fachzeitschriften auf InoFlex von HWR Spanntechnik aufmerksam geworden und haben mich auf diese Möglichkeit hingewiesen“, erklärt Manz. „Wir fanden das Konzept überzeugend und wollten es sofort in der Anwendung testen.“ Infolgedessen nahm Stöber Kontakt mit HWR auf. Nach einer Präsentation vor Ort in Pforzheim und einer eingehenden Beratung wurden anhand einer Werkstückzeichnung Spannbacken konstruiert. Nach der Auslieferung testete Stöber InoFlex auf Gutbefund. „Die ersten zwei Tage haben wir die Testreihe begleitet“, bemerkt Peter Pott, zuständiger Vertriebsmitarbeiter bei der HWR Spanntechnik GmbH. InoFlex konnte den Erwartungen von Stöber entsprechen und zeichnete sich vor allem durch Flexibilität und eine geringe Verformung aus: Im Gegensatz zu herkömmlichen Futtern für Drehmaschinen verfügt InoFlex über vier Spannbacken. Die sorgen nicht nur für einen besseren Halt – gänzlich unabhängig von der Form der Werkteile – sondern auch für eine weniger ausgeprägte Polygonbildung.
„Wir haben uns 2010 die Aufgabe gestellt, ein Spannmittel zu entwickeln, das die Geometrien rund und kubisch ebenso wie asymmetrische Teile spannt“, erinnert sich Volker Henke, Geschäftsführer bei HWR. „Unser Ziel war es zudem, alle wichtigen Daten wie Spannkraft, Drehzahl, Bauhöhe und Gewicht so zu optimieren, dass sie mit einem handelsüblichen 3-Backen-Futter vergleichbar sind.“ Möglich war eine Anpassung an alle Formen nur durch vier Backen, doch das Problem einer physikalischen Überbestimmtheit blieb: Wenn alle Spannbacken gleichmäßig zu einem Zentrum fahren, kann an einem Punkt keine Kraft ausgeübt werden. Eine Lösung versprach nur die ausgleichende Spanntechnik, bei der beide Backenpaare unabhängig voneinander, aber zentrisch an das Werkstück anlegen können.
Reduzierung auf nur neun Bauteile
Die ersten InoFlex Prototypen bestanden noch aus 60 Bauteilen; es war klar, dass hier noch Optimierungsbedarf bestand. Das Ergebnis umfasst nun lediglich neun Teile. Die zwei diametral gegenüberliegenden Backenpaare werden durch ein Kulissengetriebe angetrieben. Mithilfe dieser Reduzierung der Bauteile und damit folglich der Reibung kann das patentierte InoFlex durchaus mit 3-Backen-Futtern mithalten: Das bei Stöber eingesetzte InoFlex VK031, ein Kraftspannfutter ohne Durchgang, hat einen Hub von 9,6 mm, eine maximale Spannkraft von 182 kN und eine Drehzahl von 2.800 pro Minute. Mit anderen Modellen sind sogar Spannkräfte bis zu 230 kN möglich.
Durch die flexible Aufnahme ist InoFlex in Dreh- und Fräsmaschinen sowie in kombinierten Maschinen einsetzbar. „Die Möglichkeit der Nutzung an verschiedenen Maschinen war ein wichtiger Punkt für uns“, bestätigt Manz. „Auch sollten verschiedene Backenformen einsetzbar sein.“ Zudem konnte dank der Erweiterung von drei auf vier Backen eine deutlich reduzierte Verformung und eine hohe Rundlaufgenauigkeit erreicht werden. Auch die Wiederholgenauigkeit wurde verbessert: „Mit vier Spannpunkten lassen sich sehr enge Toleranzen erreichen“, führt Henke aus.
Formgenauigkeit deutlich verbessert
Durch die geringe Verformung beim Spannen der Werkstücke und der zentrischen Spannung auch bei asymmetrischen Rohteilen konnte die Qualität der Endprodukte bei Stöber deutlich gesteigert werden: „Insbesondere die Formgenauigkeit im Lagersitz ist jetzt deutlich gestiegen – sie liegt im Bereich 6 μm und besser“, bemerkt Manz von Stöber. Außerdem spielen jetzt Unterschiede zwischen den Rohlingen keine Rolle mehr, Parametrierungen beim Wechsel der Gussnester entfallen. Auf diese Weise konnte der gesamte Prozess optimiert werden, vom Arbeitsvorgang über die Prozesssicherheit bis hin zum Endergebnis.
Bisher sind keinerlei Probleme aufgetreten. Um eine lange Haltbarkeit zu garantieren achtet HWR auf hochwertige und gut verarbeitete Werkstoffe: Alle Teile sind gehärtet und anschließend hartbearbeitet beziehungsweise geschliffen. Zusätzlich sind alle Spannmittel FEM berechnet und somit dauerfest. „Darüber hinaus testen wir an einem eigenen Prüfstand all unsere Spannmittel auf Dauerfestigkeit“, so Henke weiter. Von der Qualität ist auch Stöber überzeugt: Inzwischen sind in der mechanischen Fertigung des Unternehmens zwei InoFlex im Einsatz, ein Angebot für ein drittes Modell wurde bereits erstellt.