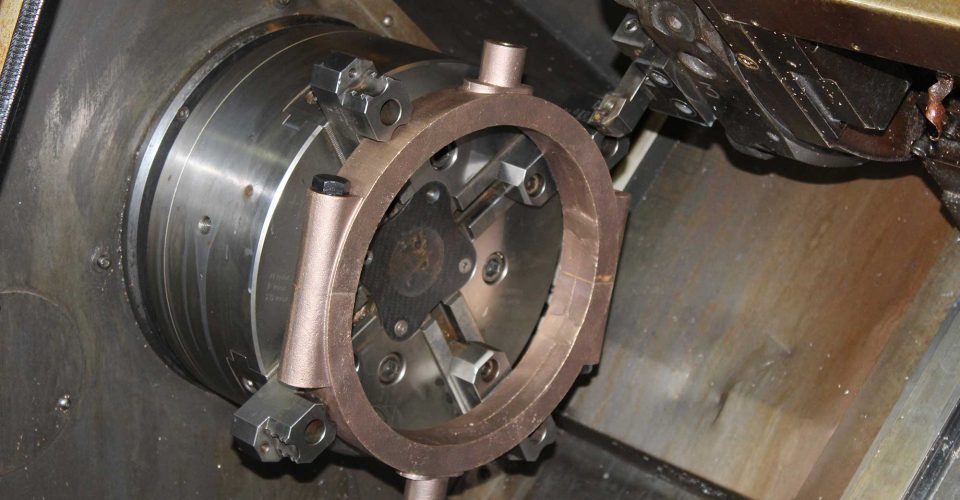
Ein spannender Erfolg
Als 1996 die Andreas Meier Zerspanungstechnik gegründet wurde, zeigte sich sehr schnell die zukünftige Ausrichtung des Unternehmens: Die Bearbeitung von Guss- und Brennteilen als Lohnfertiger. 12 Mitarbeiter, davon zwei Auszubildende, produzieren mittels Dreh- und Fräsbearbeitung die herausfordernden Werkstücke, mit denen sich das Unternehmen einen Namen gemacht hat.
Es war für ihn aufgrund seiner Zeit als Meister in der Zerspanung sofort klar, wie Andreas Meier heute sagt, dass er von seinem damaligen Arbeitgeber die mechanische Bearbeitung übernehmen würde. Seine ersten Aufträge verlangten wegen des Rohmaterials aus Guss sofort Besonderes vom jungen Unternehmer: Zum einen wurden viele verschiedene Spannmittel benötigt, wie Zwei- Drei- und Vierbackenfutter, weil die Maschinen flexibel genutzt wurden. Eine erhebliche Kostenbelastung in der Beschaffung, aber auch in Bezug auf Rüst- und Spannzeiten. Zum anderen mussten Vorrichtungen eigens angefertigt werden für all das, was nicht in einem Futter gespannt wurde. Da gerade in der Anfangszeit die Serien von der Stückzahl eher klein waren, war auch hier eine produktive Fertigung nur sehr schwer möglich.
Große Herausforderungen für das junge Unternehmen
Die Qualität der Werkstücke war ebenfalls schwierig zu gewährleisten, da die Dreibackenfutter das Bauteil oftmals polygonförmig verformten und somit die Toleranz komplett ausgenutzt wurde. Beim Einsatz von Vierbackenfuttern kam es wegen der Rohteiltoleranzen teilweise zu einer Überkompensation der Spannbacken. Dadurch hatten im schlimmsten Fall nur zwei von vier Spannbacken das Bauteil im Griff. Die instabile Aufspannung führte zu schlechten Oberflächen und unwirtschaftlichen Schnittbedingungen. Die Nutzung von Ausgleichsblechen zwischen Bauteil und Backe dagegen führte zu langen Werkstückwechselzeiten und war somit unproduktiv. „Bauteile wurden während der Bearbeitung sogar aus dem Futter gerissen“, erklärt Andreas Meier, „was zum Teil zu größeren Maschinenschäden führte.“
Das Spannen der Werkstücke war nicht zufriedenstellend zu lösen
Selbst bei wiederkehrenden Bauteilen wurde, je nach Güte des Halbzeugs, mit völlig verschiedenen Technologiewerten gearbeitet. Und das flexibel mit Gussteilen aus Aluminium, Edelstahl, Rotguss, Messing, Stahlguss und Grauguss nebst verschiedenen Brennteilen aus Stahl. Auf den sechs CNC Drehmaschinen und zwei CNC 4- und 5-Achs-Bearbeitungszentren leisteten die in zwei Schichten arbeitenden Mitarbeiter Enormes.
2013 jedoch entdeckte Andreas Meier beim Besuch der EMO in Hannover das Spannfutter INOFlex®. Große Rohteiltoleranz, flexible Konturen, Spannen auf Entformungsschrägen und Brennkanten sowie einfaches Spannen verformungsempfindlicher Bauteile: dieses Futter könnte sämtliche Herausforderungen der Bearbeitung lösen. Mit Handspannung war das INOFlex® für Andreas Meier an den CNC Drehmaschinen aber noch nicht einsetzbar.
INOFlex® heißt die perfekte Lösung für komplizierte Aufspannungen
Sobald das System INOFlex® VK (Kraftspannung) zur Verfügung stand, wurde in der Größe 315 mm ein Exemplar kurzfristig beschafft und nach anfänglichen Bedenken von den Mitarbeitern durchgehend eingesetzt. Schon bei der Bearbeitung des ersten Bauteils wurden Verbesserungen sichtbar: Weil beim INOFlex® Futter alle Backen auch bei maßlicher Abweichung des Bauteils immer mit der gleichen Kraft spannen, konnte die Bearbeitungszeit von 18 auf 9 Minuten reduziert werden. Die verringerte Neigung zu Schwingungen sorgte für eine verbesserte Oberflächengüte trotz höherer Vorschübe. Und weil das betreffende Bauteil verformungsempfindlich war, zeigte die um den Faktor 9 verbesserte Rundheit, wie sehr INOFlex® die Mehrmaschinenbedienung vereinfachen würde.
Die anderen Spannmittel haben beinahe ausgedient
Ein 2-Backenfutter wird inzwischen im Betrieb nicht mehr benutzt, weil mit INOFlex® eine 2- Backenspannung ohne Futterwechsel realisierbar ist. Wenn möglich wird auch auf das Dreibackenfutter verzichtet, da etwa 90 Prozent der Teile dank INOFlex® mit kürzerer Rüstzeit gespannt werden können. Durch die ausgleichend spannende Technik des Futters werden weniger Spannbacken benötigt, was auch die Kosten bei der Spannbackenbeschaffung senkt. Auf die Vorteile des neuen Spannmittels aufmerksam geworden, wünschten auch die Mitarbeiter der Kleinteilbearbeitung ein INOFlex® Futter in der Größe 210 mm, was kurze Zeit später beschafft wurde und jetzt die gleichen Erfolge realisieren kann.
INOFlex® mit Durchlass für unkomplizierte Drehteilbearbeitung
Da bei Andreas Meier auch Bauteile bearbeitet werden, die in einem Futter mit Durchlass gespannt werden müssen, hat er auch die neueste Entwicklung von HWR getestet: das INOFlex® VT, Kraftspannung mit Durchgang. Dieses Spannfutter senkte den täglichen Programmieraufwand erheblich und das bei gleichbleibender Qualität und Sicherheit der Bauteilspannung. „Wäre das Spannfutter INOFlex® vor 10 Jahren erhältlich gewesen, hätte ich kein Zwei-, Drei- oder Vierbackenfutter mehr im Hause und jede Drehmaschine wäre mit INOFlex® ausgerüstet“, hält Andreas Meier fest. Da bereits jetzt über die Beschaffung neuer Maschinen in 2017 nachgedacht wird, ist für den Unternehmer bereits eines klar: „Es kann über alles diskutiert werden, aber das Spannfutter wird ein INOFlex® von HWR.“